WHAT IS FATIGUE ANALYSIS ?
Fatigue is the progressive deterioration of structures under repeated loading. Microcracks appear on the material's surface and can grow, causing structural failure.
Detecting and assessing fatigue is crucial for ensuring the safety and reliability of structures under real load conditions.
Fatigue analysis is a standard step in structure design and especially for metal structures( …)
Environmental loads (for example sea states, wind states or marine current states for an offshore wind turbine) have large impacts on infrastructure and play a leading role in structural fatigue. Metal or reinforced concrete based structure are also very sensitive to corrosion and temperature gradients affecting their structural behavior.
By processing fatigue from stress estimation, the Digital Twin pinpoints the remaining life of a structure
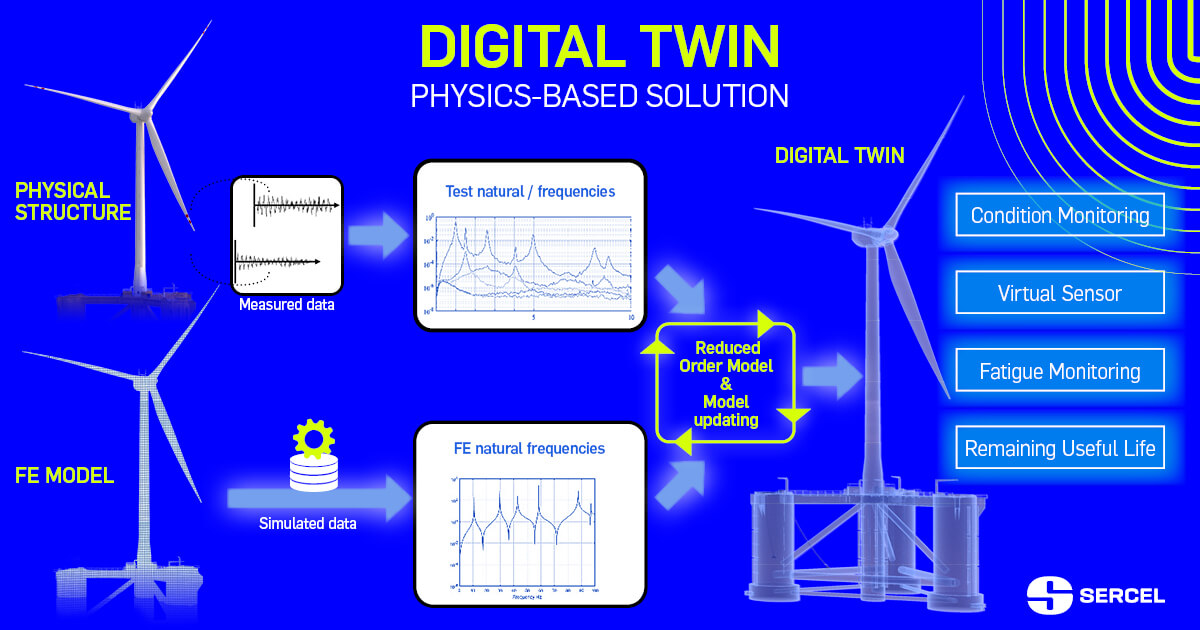
WHAT IS REMAINING USEFUL LIFE ESTIMATION ?
Remaining Useful Life is the expected duration an asset will operate before requiring repair or replacement.
RUL is predicted life-span of components or system based on projection into the future of historical load conditions experienced by the structure.
This indicator estimate how much time a component or system has before it fails.
This information is important for various purposes :
- Maintenance scheduling
- Optimize maintenance and costs
- Avoid unplanned structure downtime
WHAT IS THE PROCEDURE FOR ANALYZING FATIGUE ?
The procedure for analyzing fatigue involves several key steps to ensure a comprehensive assessment :
- Data Collection:
Data is collected on material properties, geometric specifications, and the operating conditions to which the structure is subjected.
It's necessary to install sensors directly on your structures to collect reliable data : accelerometers for structural measurements and environmental sensors for loads measurements.
During the life of a structure, external conditions affect the structural condition of the asset. These external factors can change over time.
It's essential to be able to analyze them, such as load conditions, load frequencies, and load types...
- Stress Analysis:
Constraint analysis allows to anticipate the various possible scenarios and gain a comprehensive understanding of structure's weaknesses.
This analysis is essential for identifying areas of stress concentration and estimating fatigue levels.
- Fatigue Life Processing :
To estimate the level of fatigue, fatigue methods such as DNV, EUROCODE or FKM recommended practice or guide are used. The fatigue properties and stress levels of the materials used in the process must be considered.
- Monitoring and Testing:
Monitoring systems, such as s-morpho system, allow structural performance to be tracked in real time.
Tests are performed under controlled conditions and can provide invaluable information about the variable loads on a structure.
- Modeling with Digital Twin Technology:
The creation of a digital twin is based on a virtual replica of the structure, continuously calibrated with real measurements on the structure.
This modeling enables accurate analysis of structural fatigue. The digital twin enables the detection of potential failure points, by for example estimating stress all along the structure.
- Predictive Maintenance Strategies:
Predictive maintenance techniques aim to assess the state of in-use equipment, enabling accurate predictions of maintenance needs. This strategy ensures cost efficiency by conducting maintenance activities based on actual requirements, rather than fixed schedules.
Fatigue analysis enables predictive maintenance planning. Maintenance should be planned before critical damage occurs. These actions are essential to optimize the service life of assets.
- Continuous Improvement:
Structural fatigue analysis also enables a process of continuous improvement. Through real-time monitoring, model data is updated to ensure consistent reliability and safety of the structure throughout its life cycle.
HOW IS REMAINING USEFUL LIFE CALCULATED ?
Remaining Useful Life (RUL) is calculated by systematically assessing the current performance and past condition of the asset.
This calculation involves analyzing data gathered over time from the asset's usage, operational conditions, and maintenance records.
RUL is estimated from damage and fatigue. Damage and fatigue are processed using standard methods such as Eurocode, DNV recommended practices or FKM guide, the same used for structure’s design.
Through a comprehensive evaluation of these factors, one can derive an estimate of the remaining time or usage during which an asset is expected to function effectively before necessitating replacement or facing failure.
WHAT IS THE PREDICTIVE MAINTENANCE ?
Predictive maintenance programs aim to anticipate and address potential equipment failures before they happen. By pinpointing performance inefficiencies and indicating impending issues, these programs optimize equipment performance and minimize downtime. This targeted maintenance strategy not only reduces the need for frequent inspections and repairs but also facilitates early intervention, mitigating the risk of more severe and costly problems in the future.
Type of maintenance :
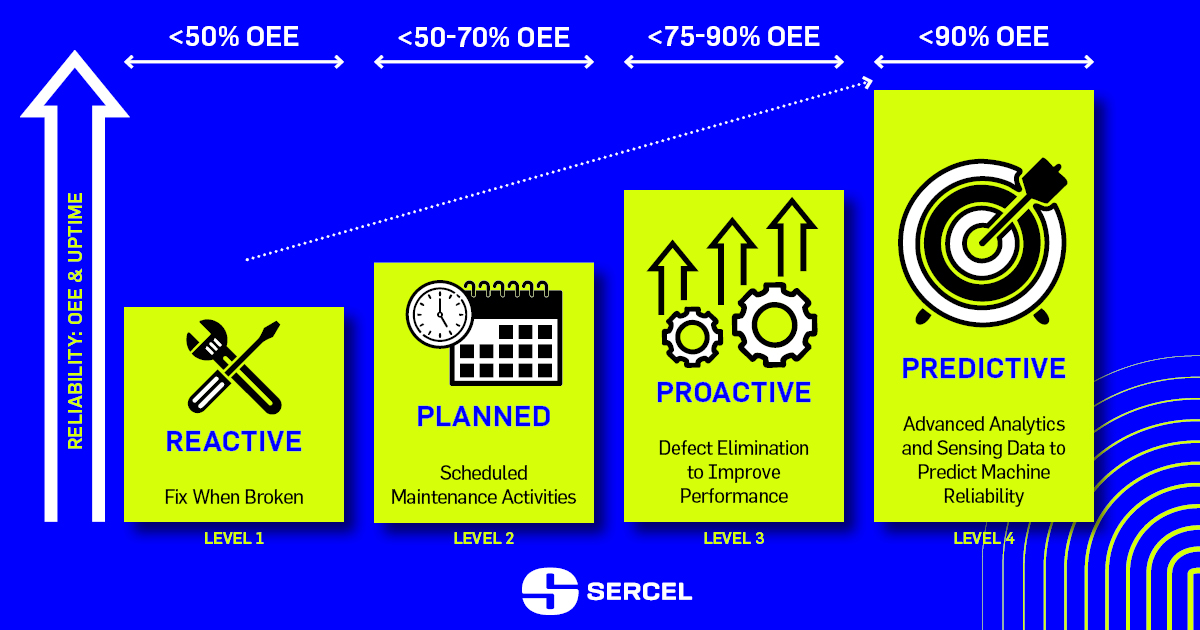
OEE: Overall Equipment Effectiveness
WHAT ARE THE BENEFITS OF PREDICTIVE MAINTENANCE ?
Reduced maintenance costs:
• Predictive maintenance helps identify potential issues before they cause breakdowns, helping to avoid costly repairs and unplanned downtime.
• Indeed, by planning maintenance interventions, it is possible to minimize labor and material costs.
• Additionally, predictive maintenance can extend the life of equipment, reducing replacement costs.
Improved equipment reliability:
• By continuously monitoring the condition of equipment, predictive maintenance helps detect problems as they arise, allowing corrective action to be taken before problems become worse.
• This helps improve overall equipment reliability and reduces the risk of critical failures.
Increased productivity:
• By reducing unplanned downtime, predictive maintenance helps improve overall equipment productivity.
• This can result in increased production, better product quality and reduced delivery times.
Improved security:
• Predictive maintenance can help prevent accidents and injuries by identifying potential safety issues before they cause damage.
• This can create a safer working environment and reduce costs related to workplace accidents.
Better planning of maintenance interventions:
• Predictive maintenance allows maintenance interventions to be planned more proactively, helping to optimize resource utilization and reduce production disruptions.
• It can also help improve customer satisfaction by reducing the number of unexpected outages.

Discover Digital Twin Technology
- Operational Modal Analysis (OMA)
- Static Deformation Reconstruction
- Digital Twin Development
- Fatigue study algorithm