HOW DOES A DIGITAL TWIN WORK?
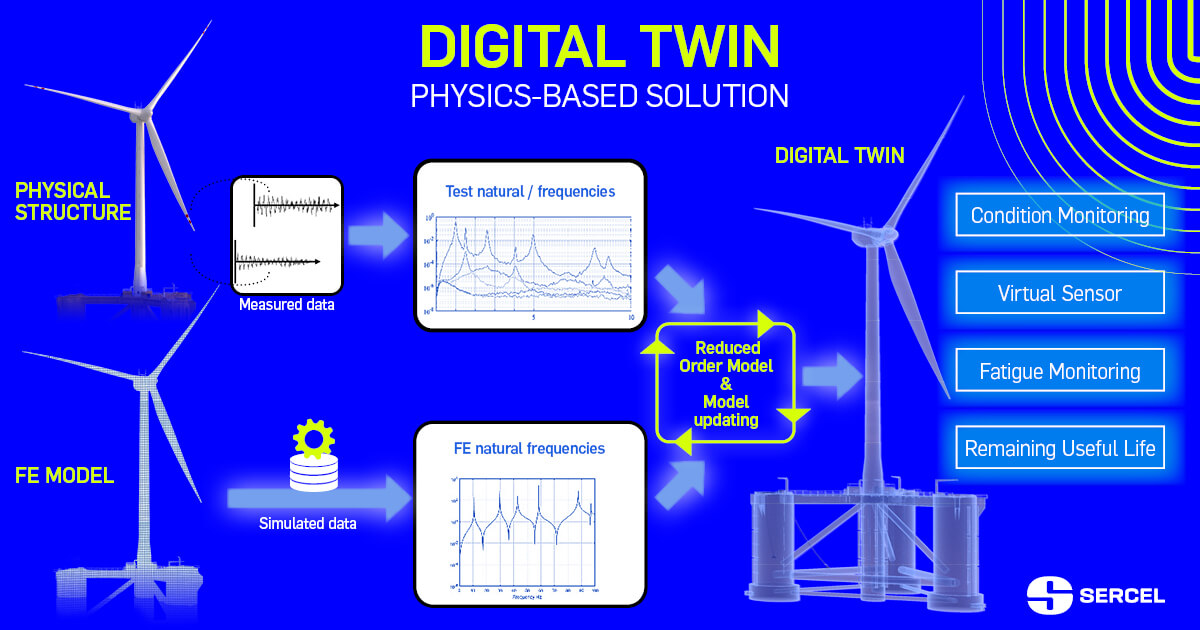
Digital Twin is a virtual model powered by two types of data:
Data from physical structures: Based on data streaming from highly reliable sensors, we can gather information about the surrounding environment and the behavior of a structure, like a wind turbine. These data make it possible to understand how the asset behaves in its environment (weather conditions, strong wind) providing real-time insights into its evolution.
Simulating Data in a virtual environment: Based on the design data of a structure, we can create a realistic and reliable virtual model (Finite Element Model: FEM) in a virtual environment. This virtual model provides simulated data using measured environmental loads of the infrastructure.
Based on the calibrated Finite Element Model, a reduced order model (R.O.M) of the relevant structure is designed : the heart of a digital twin. Feed by simulations and measurements, the Digital Twin make possible access to virtual sensors to monitor hard-to-reach areas on wind turbines.
Once this model is established, Digital Twin is consistantly updated in real time. Operating in a virtual environment capable of simulating various scenarios, the Digital Twin provides different types of outputs such as condition monitoring, fatigue monitoring (allowing estimation of damage) and force monitoring.
Digital Twin technology aims to assess the fatigue experienced by a structure over time, considering various conditions and the primary design of a structure. By analyzing fatigue decision-makers can then estimate the Remaining Useful Life (RUL) of the asset.
WHAT IS THE DIFFERENCE BETWEEN DIGITAL TWINS AND SIMULATIONS?
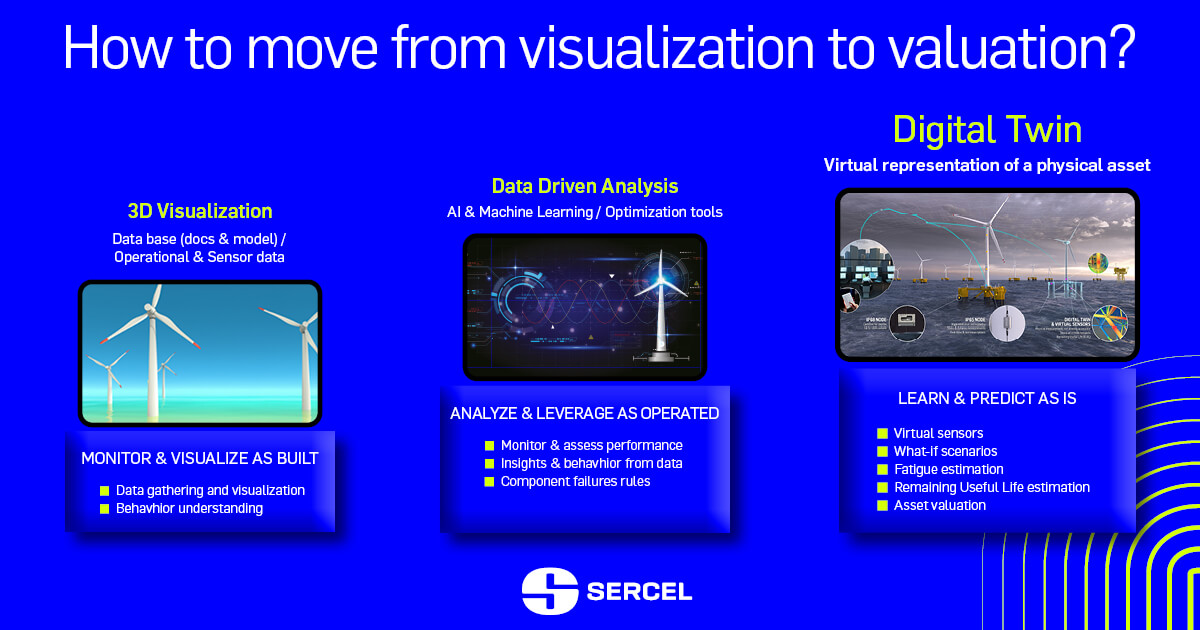
Digital Twins are often confused with traditional virtual models, but there are fundamental differences. Each type of model serves specific needs.
3D Visualization:
Generates objects in a three-dimensional space, with a focus on realistic appearance for better visual understanding. This visualization is based on Finite Element Models or similar methods.
Data-Driven Analysis:
Interprets real-time monitoring data, extracting valuable insights about the physical model in the real world. Based on AI, this analysis detects structural behavioral anomalies globally but does not consider the physical parameters of the structure.
Digital Twin technology:
Conversely, a Digital Twin is a physics-based model and is mainly made up of a reduced order model and a model updating algorithm.
Digital Twin technology predicts the fatigue and Remaining Useful Life (RUL) of a structure continuously and in real-time. It proactively identifies potential damage, ensuring strctural integrity and operational efficiency.
After creating a Digital Twin, virtual sensors can be positioned and extracted to monitor unreachable on infrastructure vulnberabilities in a virtual environment.
WHAT ARE THE BENEFITS OF A DIGITAL TWIN TECHNOLOGY?
Digital Twin brings several operational benefits:
Enhanced Asset Performance: Digital Twin empowers continuous analysis of physical system behaviors, enabling the identification of potential problems and implementation of corrective actions to optimize asset performance and efficiency.
Predictive Maintenance: By gathering detailed structural insights, Digital Twins improve risk management and enable proactive maintenance actions to address potential needs before they cause downtime or damage.
Asset Life Cycle Estimation: Real-time monitoring enables the assessment of the stress and fatigue experienced by an asset over time, providing valuable information for estimating its Remaining Useful Life and making informed decisions about asset replacement or refurbishment.
Early detection of anomalies: Digital Twin excels at early detection of anomalies, allowing for timely and cost-effective repairs to minimize maintenance expenses and prevent costly downtime.
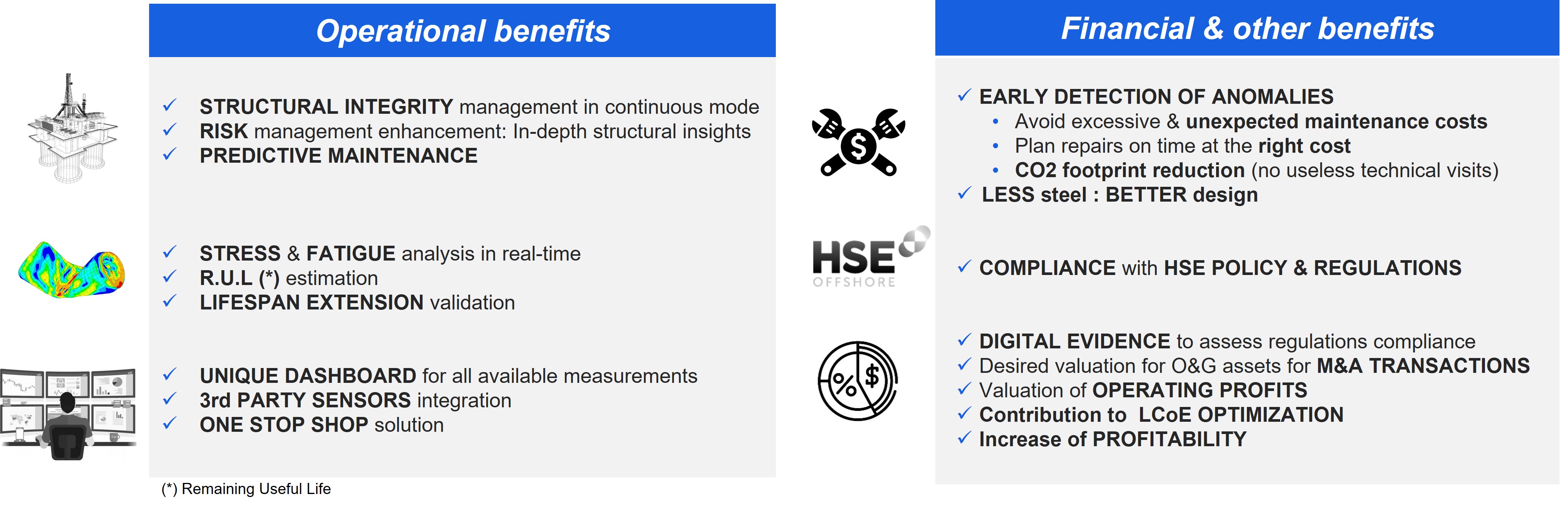
WHAT ARE MARKETS FOR DIGITAL TWINS?
Digital Twin technology revolutionizes the offshore wind sector, enhancing wind turbine and foundation design efficiency while mitigating maintenance costs and reducing carbon emissions.
- Oil and Gas sector: Digital Twin technology proactively identifies structural anomalies, analyzes stress and fatigue levels to assess asset lifespan and optimizes maintenance schedules, to ensuring efficient operations.
- Manufacturing sector: leads the way by adopting Digital Twin technology, utilizing it actively to simulate production processes, pinpoint bottlenecks and streamline workflows.
- Healthcare sector: There's a signifiant investment in Digital Twin technology. It actively simulates surgical procedures, increasing patient safety. These digital counterparts also model the impact of novel treatments on the human body, pinpointing the most promising options. Moreover, they actively aid in gathering and analyzing patient data, fostering personalizedcare tailored to individual needs.
- Transport sector: embraces Digital Twin technology for dynamic traffic optimization. It actively simulates traffic scenarios, identifies congestion points and actively fine-tunes.
Futhermore, Digital Twin play an active role in enhancing vehicule safety by actively simulating driving conditions, identifying risks and actively supporting the development of cutting-edge safety systems. The Digital Twin also activelycontributes to advancing autonomous vehicles by simulating behaviors in various conditions, actively promoting the creation of safer and more efficient autonomous vehicles.
Digital Twin technology also plays a pivotal role in optimizing Levelized Cost of Energy (LCoE) and estimating Remaining Useful Life in all market utilizing Digital Twin.
WHAT IS THE HISTORY ORIGINS OF DIGITAL TWIN?
The concept of the "Digital Twin" originated in 1960 during NASA's Apollo 13 mission. In response to an oxygen tank explosion and engine damage, NASA actively used various simulators to analyze the failure. They extended a physical asset model by integrating digital components, marking the birth of the first "digital twin".
The impetus for the design and creation of digital twins can be traced back to David Gelernter's 1991 book "Mirror World". However, it wasn't until 2002 that Michael Grieves formally introduced the concept to the public. He actively presented his first digital twin model at the Society of Manufacturing Engineers in the dissemination of this groundbreaking idea.