The move from analog to digital technology has happened gradually rather than suddenly in the seismic industry, with the first digital seismic sensors based on microelectromechanical systems (MEMS) accelerometers launched almost 20 years ago. Since then, these small and highly-accurate devices have undergone continued technological development, to the point where they now offer several distinct performances advantages compared to traditional geophones. Here we outline five key drivers behind the migration from analog to digital technology.
1. MEMS delivers digital fidelity
While the response of geophones is damped below their natural frequency and distorted above their spurious frequency, MEMS sensors offer linear and flat amplitude and phase responses from DC to 800 Hz in the acceleration domain. Their specifications are not affected by temperature, ageing or manufacturing tolerances, making the signal recorded accurate in both phase and amplitude on the entire seismic bandwidth of interest. The preservation of amplitudes has been recognized for amplitude versus offset applications. The coil-free design makes the sensor insensitive to electromagnetic noise, and the sensor distortion is much lower than that of geophones. This digital fidelity is viewed as a significant benefit for high trace density, single receiver surveys.
2. Low noise floor and low-frequency performance
Much progress has been made in lowering the noise floor of MEMS sensors, improving the detection of low frequencies and weak signals such as those that come from faraway targets or from micro-seismic events. The latest devices have been developed to reach a target specification of 15ng/√Hz through a variety of techniques linked to mitigation of all internal electronic and mechanical noise sources without any increase in power consumption.
These days, MEMS sensors achieve a significantly lower noise floor than previously available designs, achieving -10dB and thus a higher dynamic range in the region of +10 dB, providing ideal conditions to record low frequencies down to 1Hz. Also, recent research shows it is possible to develop MEMS accelerometers with a noise floor below New High Noise Model down to 0.1Hz and showing only a slight increase down to 0.001 Hz, opening up new possibilities for below hertz signal recording.
3. 3C recording and vector fidelity
3C acquisition has a proven track record of success in complex geologies. From an operational perspective, the 3C MEMS channel is omni-tilt and compact, and removes potential errors when connecting geophones to three digitizers. The same sensor can be used for the three components, while geophones must be compensated for gravity when operated horizontally. The MEMS tiny size allows for a correspondingly small housing form-factor, thus enabling an efficient rejection of parasitic signals, such as ground-roll induced rotations. The compactness of the 3C sensor also favours optimal coupling to the ground – a paramount factor for the proper recording of horizontal components.
Another significant benefit of 3C MEMS lies in the excellent vector fidelity it provides to seismic measurements. Indeed, good MEMS accelerometers are fitted with a feedback loop that enables the measurement of static signals, such as the Earth’s gravity. Thanks to this feature, 3C MEMS sensors can be easily factory-calibrated by using a very accurate gravitational acceleration reference, and consequently, the manufacturing orthogonality tolerances of the three axes can be compensated for.
4. Operational benefits result in savings
Historically, it has always been considered that a configuration of MEMS-based digital sensor units is more expensive than a field digitizing unit connected to a string of geophones, mainly due to the higher density required. However, over time, the seismic industry has started to take a more holistic approach to the cost of seismic sensors, with greater recognition of the difference between capital expenditure for equipment and operational expenditure.
The smaller physical size of MEMS-based sensors provides many operational benefits. For geophone strings, a lot of effort is required to transport, deploy, retrieve, maintain and repair large quantities of equipment – in addition to the staff needed for these tasks and the subsequent logistics such as accommodation, catering, laundry, transportation etc. The use of MEMS-based digital sensor units, on the other hand, provides savings in each of these areas.
5. Lower power and lower costs
The steady growth in popularity of MEMS-based devices has also delivered manufacturing economies of scale, which has in turn driven down the price. Also, a single sensor’s power consumption has been reduced to 85mW, which is providing costs benefits for large-scale, high-density deployments.
These benefits have seen MEMS-based sensors start to break down barriers and achieve greater market acceptance. After almost 20 years on the market, it is fair to say that digital sensors have proven their technical and geophysical effectiveness for seismic applications, leading to the introduction of recorders that have been fully optimized for seismic land operations.
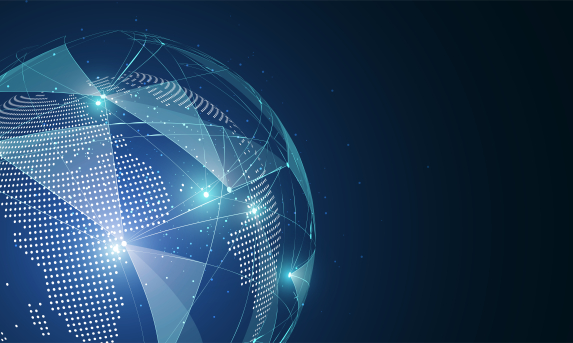